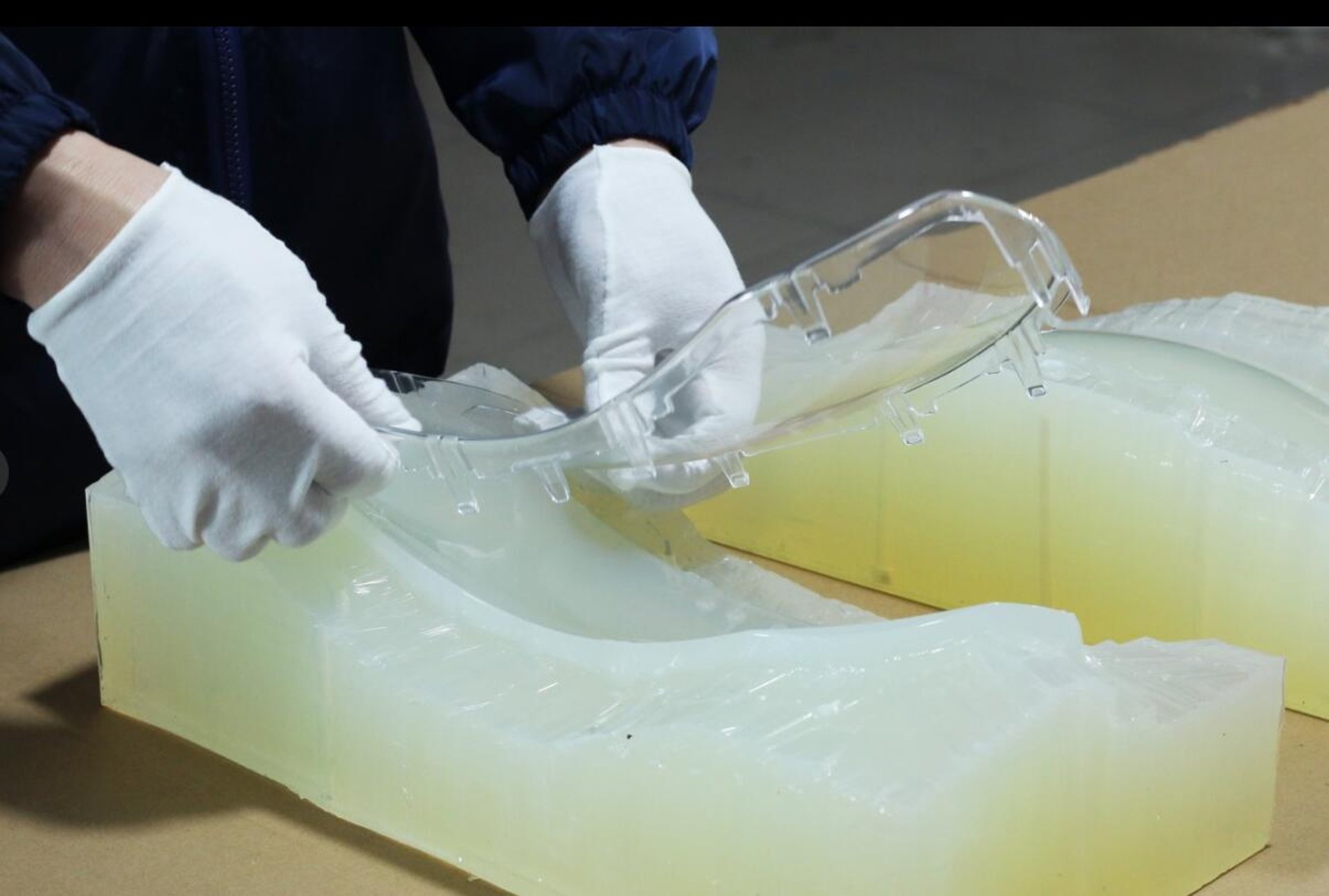
Silicone molds represent an integral facet of the manufacturing realm, employed across a myriad of industries to fashion prototypes. Employing this technique necessitates the utilization of silicone molds renowned for their elasticity and robustness, facilitating the generation of multiple meticulous replicas of a given object or component. Furthermore, these molds epitomize precision, adept at replicating intricate shapes and finer nuances with unparalleled accuracy, rendering them a favored option for prototyping endeavors. In essence, silicone molds stand as indispensable instruments in the intricate orchestration of product innovation and evolution.
VACUUM CASTING
VACUUM CASTING SERVICE
The premier choice for short-term, rapid production of low-volume plastic components. We boast the capability to swiftly engineer and manufacture plastic prototype pieces, affording our clientele the opportunity to expedite their design and development processes. Place your trust in us to expedite your project, yielding top-tier outcomes within the briefest timeframe conceivable.
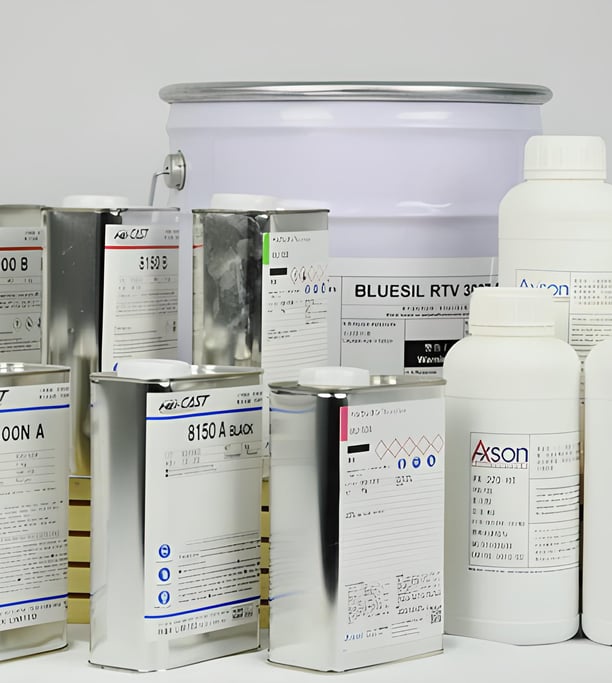
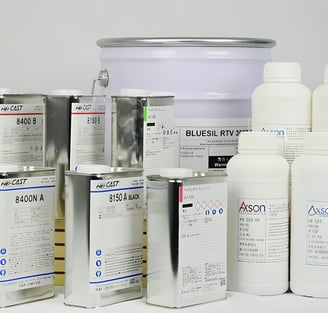
MATERIALS FOR VACUUM CASTING
Silicone stands as a widely embraced material for mold fabrication, owing to its distinctive properties. Silicone molds epitomize flexibility, durability, and heat resistance, rendering them optimal for crafting intricate and sophisticated pieces. These silicone mold materials manifest in various forms, such as liquids, pastes, or rubbers, facilitating adaptation to diverse molding needs and techniques. Furthermore, silicone is malleable and exhibits excellent adhesion to a plethora of surfaces, streamlining the creation of precise molds. These materials find extensive utility across the rubber product manufacturing, ceramic, resin, and numerous other sectors. The versatility and caliber of silicone molds render them a favored choice among manufacturers and artists alike, seeking to achieve precise and detailed results. Casting pieces can span the spectrum from transparent, translucent to colored, and from soft rubber to rigid plastic. Several materials incorporate impact-resistant glass-filled resins, high-temperature-resistant (120 ℃), or fire-resistant (UL94-V0) attributes alongside silicone of varying hardness.
Excellent surface quality and detail, similar to TPE, TPU and silicone rubber
Ideal for applications that need good shock absorption
A cost-effective way to produce prototypes or small series of end-use parts
ABS thermoplastic similarity
Excellent surface and detail, with injection molded look and feel
Flame retardant, food safe and UV stable materials available
Flexible Poliurethane
Poliurethane ABS
Poliurethane PE/PP
Thermoplastic similarity of PE or PP
Durable and lightweight with a wide range of finishes available
Excellent surface and detail, with injection molded look and feel
TECHNICAL INFORMATION
Mold Lifetime
Usual production volumes of 20-25 copies per mold are attainable. Yet, when the piece necessitates exceptional quality, such as with transparent or intricate structures, a mold might typically yield only 12 or 10 casting pieces.
Minimum wall thickness and part dimensions
Standard leadtime
Textures and other functions
The wall thickness should be at least 0.5 mm, but it's recommended to fall between 1.5 mm to 2.5 mm for optimal mold filling. With mold dimensions of 2.0m*1.2m*1.0m, the piece should maintain a 25% clearance margin.
Within the span of 7 to 10 days, the production capacity extends to a maximum of 50 units, contingent upon meticulous consideration of both mold intricacy and volume. The precise duration of the production endeavor remains subject to the interplay of these pivotal factors.
In vacuum casting, various surface textures and functions can be achieved to meet specific design requirements: Stained, textured, painted, coated, clear polished, inserts and over-molding.
Each of these techniques offers versatility in achieving desired aesthetics, functionality, and performance characteristics in vacuum casting applications.
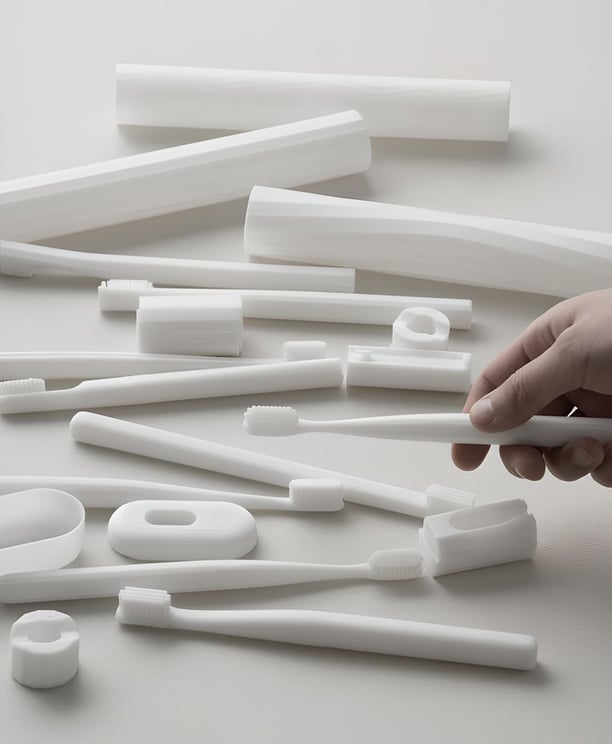
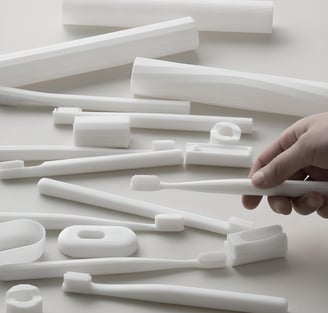
LOW VOLUME/
SHORT RUNS
In instances where production quantities fail to warrant the investment in injection molding, and there arises a need for expedited production of parts within brief cycles, an innovative recourse lies in the utilization of urethane molds. These molds afford the swift attainment of desired components weeks prior to the readiness of production tools, thereby economizing both time and expenses. Urethane molds present an apt solution for crafting parts in modest batches, delivering superlative surface finish quality. Furthermore, their inherent pliability and adaptiveness render them a versatile choice across a myriad of applications. Consequently, through the strategic deployment of urethane molds, the acquisition of requisite parts is rendered efficient and economically advantageous, even in scenarios characterized by constrained production volumes.
RECOMMENDED APPLICATIONS
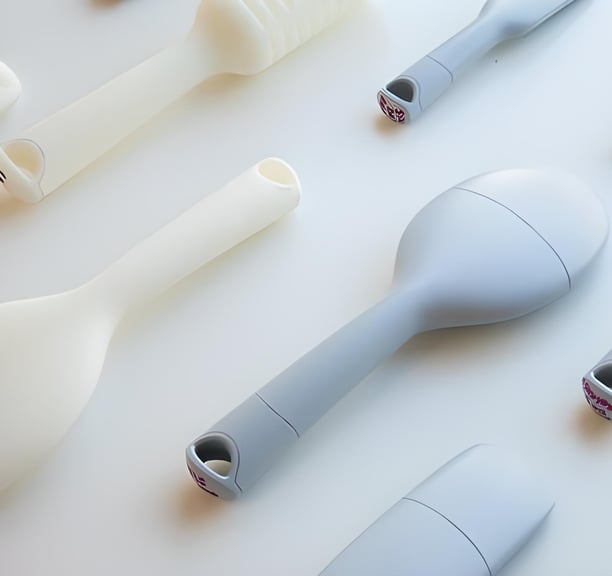
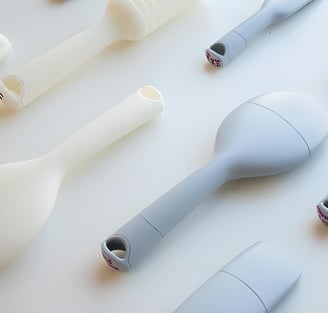
APPEREANCE PROTOTYPES/ TEXTURE AND COLOR STUDIES
Urethane casting epitomizes a dynamic aesthetic canvas, presenting an expansive array of choices spanning colors, textures, and surface finishes, all coalescing under a singular design ethos. In the quest to discern the optimal hue for the ultimate product rendition, an innovative strategy beckons: crafting a silicone mold to yield 10 to 15 cast pieces. Subsequently, each cast piece can be meticulously painted, imbuing them with the envisioned colors and textures, thereby facilitating an internal discourse to ascertain the most compelling option. This pioneering methodology not only furnishes a lucid visualization of the envisaged final product but also empowers decision-making predicated upon tangible visual cues.