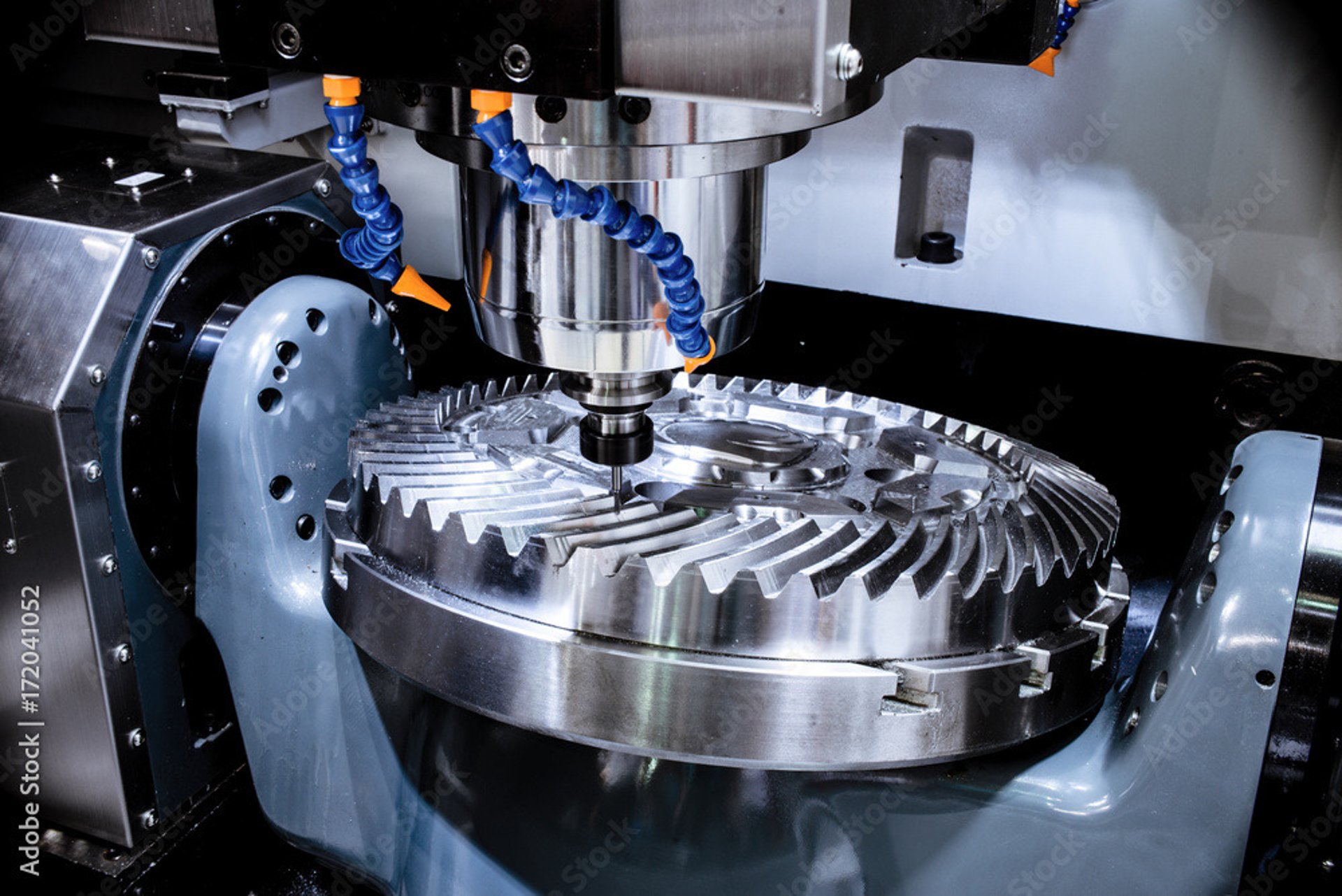
Discover the perfect machining service to craft your plastic and metal parts. Precision and quality machining are crucial for obtaining durable and functional products. Dive into a plethora of options, each tailored to your specific needs. Whether you need CNC machining, milling, turning, or any other process, rest assured you'll find skilled professionals and cutting-edge technology to ensure optimal results. Don't waste another moment—find the perfect service for your plastic and metal parts today!
CNC MACHINING
MACHINED PROTOTYPES
We provide prototype machining services for design verification and engineering testing. With a highly skilled team and state-of-the-art machinery, we execute this process efficiently and precisely. Our mission is to assist clients in validating their designs and conducting concept tests prior to mass production. We perform machining of parts using various materials, including metals and plastics, adhering to required technical specifications. Leveraging our industry expertise, we deliver quality outcomes and meet set deadlines. Committed to client satisfaction, we work closely with them to ensure successful goal attainment.
CNC MILLING
The CNC milling machine stands as an innovative technology revolutionizing part and mold manufacturing. This subtractive manufacturing method employs a cutting tool that moves and rotates to remove material, yielding high-precision components in various materials such as plastic and metal. Thanks to its versatility, CNC milling machines find extensive applications across diverse industries requiring precision parts, including automotive, aerospace, and electronics. Furthermore, these machines excel in mold creation, rendering them indispensable in the manufacturing sector.
CNC TURNING
CNC turning stands as a refined machining process utilized for material removal from a rotating workpiece. In this method, a cutter engages with the workpiece, and through meticulously controlled movements, the desired shape is crafted. CNC turning proves particularly adept at fashioning rounded or tubular forms. Moreover, this process enables the fabrication of intricate external geometries and internal holes, including the machining of various thread types. Thanks to the high velocity of the rotating workpiece, CNC turning emerges as an efficient and precise technique embraced across a myriad of industrial applications.
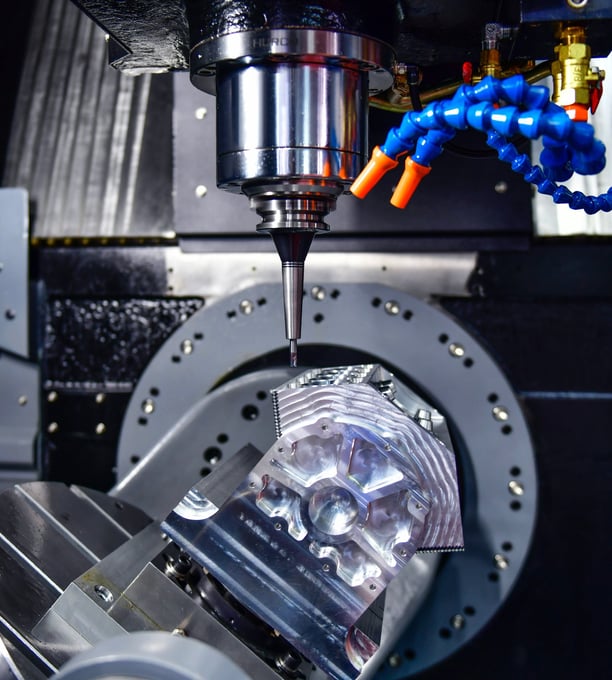
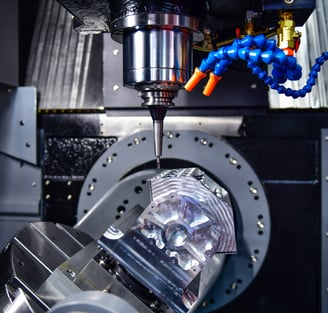
5 AXIS CNC
The 5-axis CNC machining represents an elevated technique that furnishes the capacity to fabricate intricate parts with multiple lateral features in a singular setup. This implies the processing of up to five sides of the part concurrently, thereby heightening efficiency and diminishing production times. Such machining proves particularly invaluable in crafting components for the aerospace, automotive, and medical sectors, where exacting levels of precision and quality are imperative.
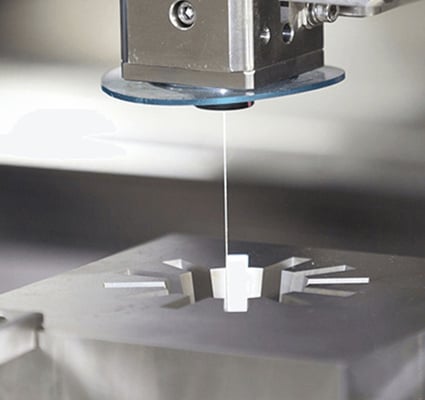
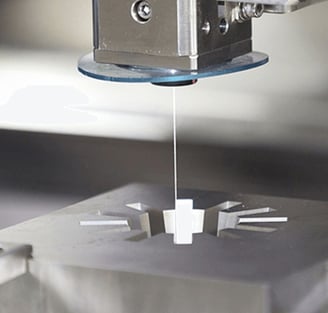
WIRE CUT (EDM)
The Electrical Discharge Machining with Wire (EDM), sometimes referred to as wire cutting or wire EDM, represents a refined method of electrical discharge machining. Diverging from the sinker EDM process, wire cutting employs a slender wire thread as its tool; however, akin to all forms of electroerosion, there exists no physical contact with the workpiece. This wire thread swiftly traverses at high velocity, instigating an electric arc that precisely severs the material. Renowned for its unparalleled precision, this technique finds predominant utilization within the industry for cutting both robust and delicate materials.
ADVANTAGES
COMUNICATION
CONSISTENCY
PRECISION
PUNCTUALITY
Parts can be manufactured within a minimum of 24 hours, enabling faster design iterations and speed to market.
Our precision machining service for low and high-volume production ensures repeatable and consistent outcomes.
We can produce parts with intricate shapes, tight tolerances, and close radius. Our precision-focused approach drives us to continuously tackle optical components with meticulous detail.
In our business, we pride ourselves on providing personalized support and commit to delivering our products promptly, with a 95% delivery rate and parts shipped within 7 days or less.